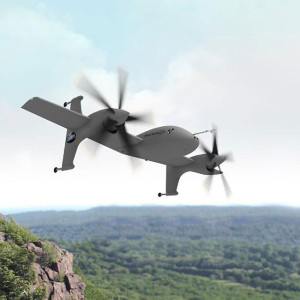
DARPA has awarded $30 million of a planned $47 funding allocated for preliminary design for the ‘VTOL X-Plane’, an experimental aircraft that can fly at high speed, hover, and take off and land vertically (VTOL). The U.S. Defense Advanced Research Projects Agency (DARPA) awarded two contracts funding 22 month programs at Sikorsky Innovations, and Aurora Flight Sciences, for the preliminary development of new X-Planes. The program goal is to build and fly a demonstrator aircraft with first flight anticipated in the fourth quarter of 2017. The overall VTOL X-Plane program is a 52-month, $130 million effort to fly an experimental aircraft capable of exceeding 300 kt., with a hover efficiency of 75 percent or better and a cruise lift-to-drag ratio of 10 or more. According to DARPA, $47 million have been allocated for several phase I contracts, with more winners to be announced soon. Following the two-year preliminary design, the second phase of the program will focus on design, development and integration, to be followed by flight-testing in phase III.
“We anticipate that DARPA will release up to four Phase 1 awards, so this is a significant win for Sikorsky Innovations.” said Mark Miller, Sikorsky’s Vice President of Research & Engineering, “we have a non-traditional technical solution, and this is an opportunity for Sikorsky Innovations to excel, to expand our relationship with DARPA, and to embark on a great partnering opportunity with another company known for its innovative solutions – Lockheed Martin’s Skunk Works.” Sikorsky Innovations is the technology development organization of Sikorsky Aircraft Corp.
With the VTOL X-Plan DARPA plans to set a new standard for vertical take of and landing aircraft, which have relied over the past 60 years on the rotorcraft concept. The speed of conventional rotorcrafts is inherently limited to 150-170 knots, which make platforms susceptible to enemy fire. Although new VTOL designs, such as the tilt rotor, succeeded in increasing the speed of VTOL aircraft, they also incurred increased weight and reduced payload capacity, while significantly increasing design complexity.
With VTOL X-Plane DARPA hopes to challenge industry to innovate engineers to create a single, hybrid aircraft that would concurrently push engineers to develop aircraft capable of flying at higher speeds, (300-400 kts), hover and cruise more efficiently than helicopters (75% improved hover, up from 60%, 10% lift to drag ratio, up from 5-6). These new platforms should retain the current helicopter payload capacities, carrying payloads weighing about 40% of the gross weight.
“We have not made this easy” said Ashish Bagal, DARPA program manager for VTOL X-PLANE. “Strapping rockets onto the back of a helicopter is not the type of approach we are looking for. This time, rather than tweaking past designs we are looking for true cross-pollinations of designs and technologies from the fixed-wing and rotary-wing worlds”.
During Phase 1, Sikorsky Innovations and Lockheed Martin’s Skunk Works will conduct trade studies and develop the initial design. For that project Sikorsky Innovations has teamed with Lockheed Martin’s Skunk Works for the VTOL X-Plane development of its Unmanned Rotor Blown Wing concept. This concept represents a unique integration of fixed wing aerodynamics and advanced rotor control, addressing DARPA’s requirement for reduced complexity of such platform.
Sikorsky Innovations plans to lead the program from its Fort Worth office, leveraging talent from both Stratford, Connecticut, and West Palm Beach, Florida, engineering centers.
Boeing is also expecting to be the third to get an award for the VTOL X-Plane development, the company has already conducted some research in ducted-fan propulsion technology utilizing an unmanned vehicle powered by quad-fan configuration. A scale model of such vehicle, dubbed ‘Phantom Swift’ was developed in less than a month at the company’s ‘Phantom Works’ using rapid prototyping process. It will serve the Boeing VTOL X-Plane team as a flying laboratory.
“A picture is worth a thousand words, a flying model is worth a million words. No matter what words you put in a proposal, having hardware that you can demonstrate that they can tangibly see what’s being proposed goes a long way toward winning that proposal,” said Perry Ziegenbein, Phantom Swift’s chief engineer.
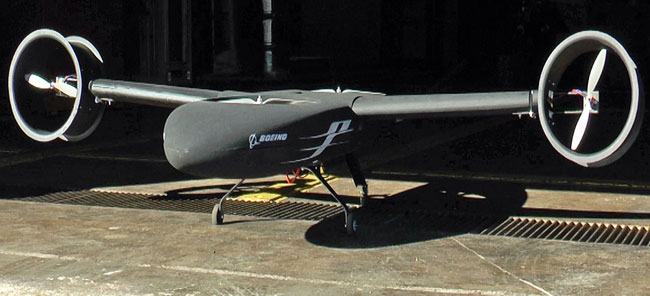
Aurora Flight Sciences has been working on a parallel program with DARPA, seeking to develop an advanced electrically powered lift fan that could be used with VTOL aircraft. Partnered with ThinGap and Trust Automation, the team’s unique approach utilizes a DC brushless ring motor, high switching rate controller, and ducted fan to deliver the required lift. The low disk loading compared to turbojets and turbofans minimizes the amount of debris kicked up during operation. The Defense Advanced Research Projects Agency (DARPA) funded contract has produced a 32-inch diameter ducted fan powered by a 70kW electric motor capable of producing over 430 pounds of thrust. The advanced aerostructure design by Aurora Flight Sciences coupled with a unique composite ring motor from ThinGap performed several thrust tests characterizing the continuous operation as well as peak performance of the integrated system. Additional testing was successfully performed using an advanced controller of Trust Automation’s design, which implemented very high switching rates and Field Oriented Control to effectively control the low inductance system. Continued development is planned to reduce weight and increase system efficiency as potential platform specific applications are pursued. This ducted electric lift technology has applications to vertical take-off and landing vehicles, helicopter tail rotors, and aircraft propulsion.
Under another program Aurora has also developed the Excalibur unmanned VTOL platform, utilizing a hybrid tilting lift fan and propulsion engines to deliver VTOL capability and high speed performance.