Military operations have changed in the 21st century, from linear, massive battles between peers, to asymmetric engagements involving unequal forces. Military against insurgents, law enforcement against terror and air power against elusive combatant elements hidden underground and immersed within the civilian population. This new type of warfare has changed the perspective of military planners. The linear battlespace of the past required combat vehicles protected by massive frontal armor, supported by unprotected logistic formations that operated away from the danger at the front line. Today’s warfare exposes all elements to threats, and requires all-around vehicle protection for the heavy forces and support elements alike; frequent increases in threat level requires constant improvements in protection.
This requirement has increased the demand for armored, mine protected vehicles for the military, law enforcement as well as other government and civilian agencies that operate in high threat environments. Such vehicles should provide an elevated level of protection and operate on roads, within the civilian environment for extended missions.
These vehicles require various levels of protection, meeting specific threat levels they may face in battle. Almost all vehicles in this class have a mix of opaque and transparent armor (TA) solutions, enabling the crew to operate the vehicle on road and in the confined spaces of an urban area. Traditionally, opaque armor is produced of steel or aluminum, that offer the thinner but heavier solution for a given level of protection; metal armor is often augmented by ceramic or composite materials to add protection and reduce weight. Lacking a transparent metal solution, TA facilitates ballistic protection through a combination of layered transparent glass and composites bonded with resins and adhesives to meet the level of protection like that provided by opaque armor. As the level of protection increases, the windows become thicker and heavier.
Developers of transparent armor are always seeking to bring lighter and thinner solutions to reduce the weight of an armor kit and increase the available volume inside the protected capsule, enabling protection for lighter vehicles.
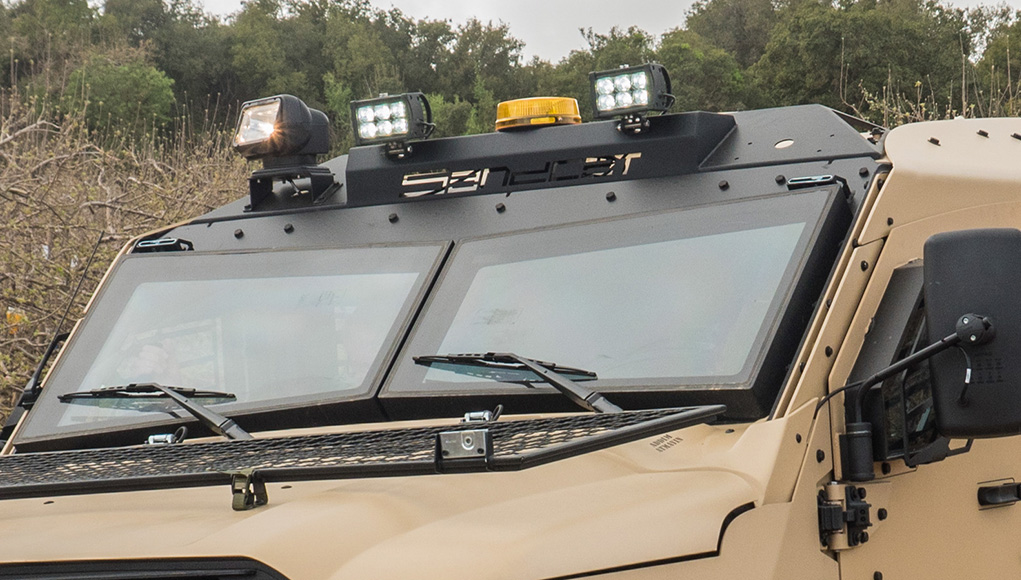
“Our transparent armor is made for both military and civilian security and defense applications.” Daniel Cohen, President, and CEO of OSG told Defense-Update. We spend significant research and development in the development of advanced TA solutions that reduce thickness and aerial weight and improve the life cycles of fielded systems. For example, OSG TA modules designed to defeat 7.62×51 mm (BR6) are 30 mm thick while OSG armor solutions defeating the 7.62×51 AP threat (BR7) are 60 mm thick. Some of our products are up to 40% lighter than previous industry standards.”
Combat vehicles are constantly exposed to harsh field environmental conditions including impact and abrasion, extreme temperature changes and humidity, and exposure to chemicals. These effects could damage the complex layered glass structure of transparent armor, causing delamination and deteriorate transparency that shortens the lifespan of the armor. As an approved supplier of TA for numerous military forces, including the USA Army, USMC, German BWB, British, French, Italian, Australian and other MODs, OSG has developed the ADI series of transparent armor that provides reduced life cycle cost.
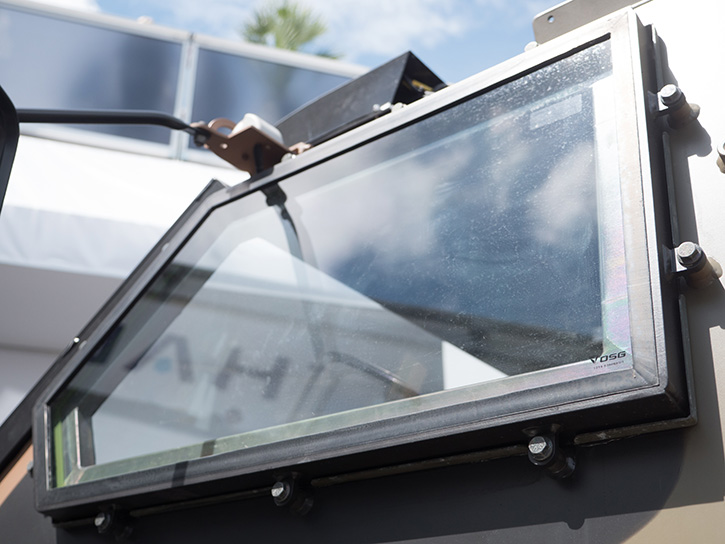
“By employing new materials and technology ADI considerably extends the durability and life cycle of the Transparent Armor, while preserving a no-spall environment within the vehicle,” Cohen said. “This armor has been proven to be lighter and stronger than “conventional” glass-polycarbonate products.” The ADI series has been extensively tested and certified for field deployment, allowing customers to benefit from easier maintenance and longer service life.
“ADI technology also offers high resistance to impact from projectiles, which allows the thickness and areal density of the product to be reduced,” Cohen added.
OSG is the largest supplier of armored windows for the MRAP and MATV family of vehicles operated by the US military and international customers. Operating with vehicle designers and manufacturers, OSG delivers optimized transparent armor solutions to meet specific requirements and platform design. The company supply such solutions to two of the latest tactical vehicles programs – the American JLTV made by Oshkosh and Australian Hawkei, made by Thales Australia.
“To meet increasing threats, we have pioneered many of our industry’s most important innovations.” Cohen said, “One of the most innovative technologies currently in development is CERALITE – an ultra-light transparent armor solution developed by OSG in cooperation with CeramTec of Germany. CERALITE transparent armor is lighter and thinner when compared to conventional transparent armor solutions at defined protection levels. It also has an increased multi-hit capability and provides better light transmission, particularly when used with night vision devices.”
Overall, CERALITE achieves greater than 50% reduction both in weight and thickness when compared to traditional glass solutions. It also improves the surface resistance to abrasion, scratches and rock impact. Reduced weight and thickness of the transparent armor also means a significant reduction in volume and therefore the weight of framing materials, further contributing to the overall reduction of gross vehicle weight. Meeting a higher level of protection at a given weight means a single transparent solution that meets all protection requirements, eliminating the need for a replacement armor (B-kit) to meet a higher level of threat. It also allows the use of a single armored windshield, contributing to better visibility for the driver. Elimination of B-kit armor represents significant cost-saving implications in design, production, operation and maintenance of the vehicle fleet across its operational lifespan. The lower weight further Improves performance, increases the vehicle’s life cycle.
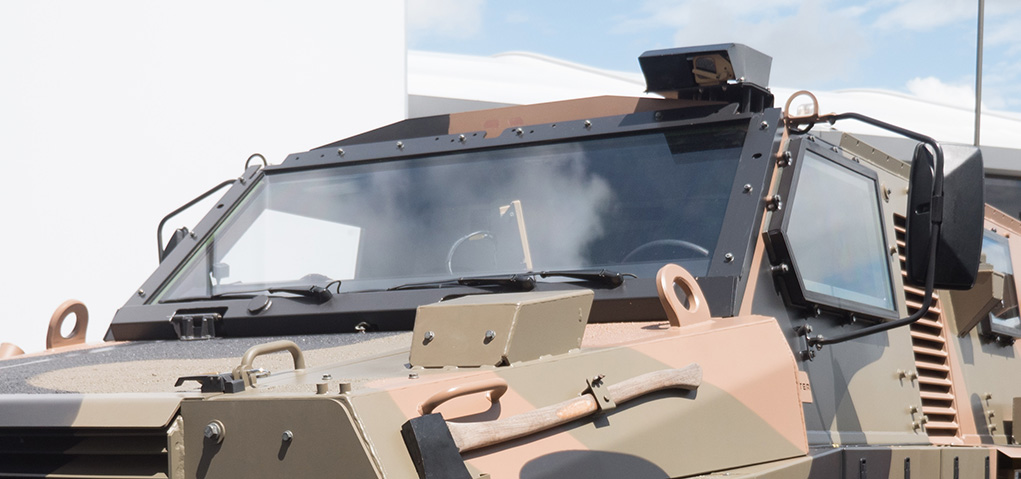