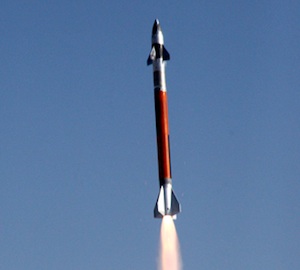
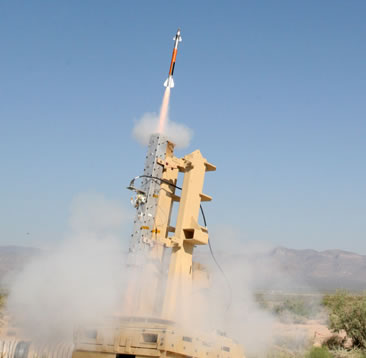
Missile maneuvering at high speed require control surfaces built to meet the extremely close geometric tolerances. Even slight deviations from design specifications can add turbulence that affects speed and trajectory, especially at supersonic speed. Even small imperfections would add turbulence that affects speed and trajectory. Manufacturers are meeting such tolerances with CNC Machining, processing each part through costly and labor intensive, inspections and measurement of each and every part.
Developing an affordable hit-to-kill weapon to intercept rockets, mortar bombs and missiles, Lockheed Martin was searching for ways to reduce each missile cost by implementing advanced manufacturing technology. Working in collaboration with Liquidmetal, the team came up with a solution tailored for the EAPS, producing the missile’s canard fins using Liquidmetal’s unique metal injection molding (MIM) technique. According to Liquidmetal, such missile control surfaces can be manufactured at a third of the cost of CNC manufacturing, and at volume prices comparable to those of conventional metal injection molding, a method unsuitable for this application.
Produced through the innovative molding process, the production cost of Liquidmetal made canard is reduced, thus affecting the cost of each round. Moreover, parts made of Liquidmetal have greater strength to weight than steel or titanium. “Lockheed Martin has been an ideal development partner for this breakthrough application for Liquidmetal Technologies, creating a high precision, high performance part at a lower cost,” said Dr. Bruce Bromage, EVP of Business Development with Liquidmetal Technologies.
Through the manufacturing process each fin is formed in a single step, injected and released from a mold where each part is precisely the same as each and every part made of the same mold. For a supersonic missile, it is critical that the top and bottom surfaces of the part be precisely symmetrical in terms of shape and weight. Liquidmetal allow typically shrinks less than 0.2%, allowing tolerances within ±0.0005” to be achieved.
Other military applications of Liquidmetal alloys include long-rod penetrators for armor-piercing munitions and conical liners for shaped charges.