
The US Navy and Marine Corps are evaluating the lessons learned from five months of operations of the Cargo Resupply Unmanned Aerial System (CRUAS) in Afghanistan and are likely to issue their recommendations for future CRUAS capability in the following phase. “Developing a standardized platform with modular components for several types of missions would capitalize on the KMAX’s reliability” said Maj. Kyle O’Connor, officer in charge, Unmanned Aerial Vehicle Squadron (VMU) 1 Cargo Detachment. Typical modular payloads could include a camera payload that would be added for an intelligence, surveillance and reconnaissance (ISR) mission; the hook and long line added for cargo pick-up; fuel pods for a long-range mission and missiles or rockets for a strike mission.
“Considering budget issues, you would want one standard platform with standard logistics, supply, training and pipeline,” he said. “The CRUAS IPT and the Marine Corps will review and analyze the after-action reports, feedback, data and theses from the Naval Post Graduate School as well as quantify the costs before making any recommendations” cautions Capt. Patrick Smith, PMA-266 program manager.
“We accomplished our mission, collected test data and proved that Cargo UAS is a viable capability,” said Maj. O’Connor of VMU-1 Cargo Detachment that flew the unmanned K-MAX K-2000 in theater. The system was deployed to AFghanistan in December 2011 and flew with VMU-1 for five months. Today, the KMAX remains deployed in Afghanistan flying missions operated by VMU-2.
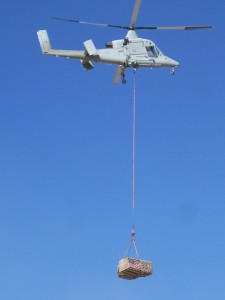
In the commercial world, the KMAX is used for firefighting, construction and lumbering. “Built as a fully operational helicopter, it requires a start-up and shut-down pilot unlike other unmanned aerial systems,” said Capt. Caleb Joiner, CRUAS mission commander. “In Afghanistan, the unmanned K-MAX flew only during the night.” Joiner said, “The two KMAX systems flew 485 sorties, or combat mission flights, for a total of 525 flight hours” he added. Most missions lasted about 1 hour and included a 20-minute turnaround time during which a pilot climbed into the helicopter to shut it down, refuel it, hook up the cargo and then start it back up. “That was a pretty short turnaround time, and allowed us to conduct six sorties per night. We could have done more,” Joiner noted. By the end of the deployment — and after receiving permission to hover — turnaround times with cargo hook-ups took 6 or 7 minutes to complete. Overall, the KMAX was very responsive, especially when compared to a convoy, a C-130 [Hercules] or an H-53 mission. According to Joiner, “Towing the KMAX out of the hangar to wheels-up, could take as little as 15 minutes.”
“Since it was an unmanned system, we were able to conduct flights during inclement weather when other helicopters couldn’t fly,” O’Connor said. “We flew during the night, in the rain, dust and some wind.” The KMAX handled up to 4,500 pounds of cargo per mission, he said. “The reliability of the KMAX was impressive, It was fully mission capable 90 percent of the time.” O’Connor said. Inclement weather accounted for 5 percent of the downtime and maintenance and scheduling issues accounted for the other 5 percent, he said. The KMAX required less than two hours of maintenance per flight hour, which equates to a low cost, O’Connor added.
Nevertheless, the operations encountered some difficulties, particularly related to coordination, airspace management and the level of flexibility in mission planning. Deployment challenges included flight clearance approvals for changes to the original plan, safety zone restrictions associated with a UAS and the over-simplicity of the operator interface, O’Connor said. Other issues raised by the evaluators included the size and weight of the UAS system containers, noisy generators that produced fumes and lack of a remote “kill switch” to turn the helicopter off. The control interface was also an issue for improvement, with the simplistic graphic user interface, (GUI), designed for an untrained Marine operators. “The highly trained operators could have handled a lot more control of the UAS,” O’Connor said. “However, we made a conscious decision to stick with the simplified system because we wanted to validate the concept as written.”
The mission of the VMU-1 detachment in Afghanistan was to fly routine, scheduled cargo UAS missions to build flight hours and gather reliability, and to support the needs of the Marine Corps by delivering cargo via an external sling load. The result was a capability that exposes fewer warfighters to the risk of roadside improvised explosive devices (IEDs) and hostile fire. “This is a great example of integration while fulfilling the ‘urgent needs’ of the warfighter,” said NAVAIR Commander Vice Adm. David Architzel as he opened the seventh Meet the Fleet post-deployment debrief here July 10. “Every time you can eliminate even a portion of a convoy, you eliminate the possibility of someone losing their life from an IED on the roads.”
The CRUAS IPT’s response to the Marine Corps’ urgent need to prove the viability of a cargo UAS and deploy the first cargo UAS within 11 months from contract award has won two accolades. The project’s speed and success earned the team an acquisition excellence award from the Office of the Secretary of the Navy in June 2012 and a Naval Air Warfare Center Aircraft Division Commander’s Innovation Award in December 2011.