Israel’s armor specialist Plasan showcases broadened product line at Eurosatory, introducing a blast-protected model of the SandCat along with several light armored vehicles. In the heavier weight classes, Plasan provides a peek into the advanced protection technologies being integrated into newly designed combat vehicles.
“Along with the four new vehicles presented in our outdoor display, our indoor display showcases our philosophy of vehicle survivability and protection, using a technology demonstrator that employs Augmented Reality (AR) to depict how the different armor technologies are implemented in new and retrofitted armored vehicle designs.” Shahar Kedem, Director, Combat Vehicles Survivability at Plasan told Defense-Update.
These elements include passive and advanced reactive armor, and various structures designed to defeat RPGs, or blast deflecting shapes, energy absorbing crushing structures and a floating floor, minimizing the underbelly or side attack blast effects. Inside the vehicle, energy attenuating seats, and various spall liners that minimize the risk to occupants in case of mine blast, IED explosion or overmatching threat penetration.
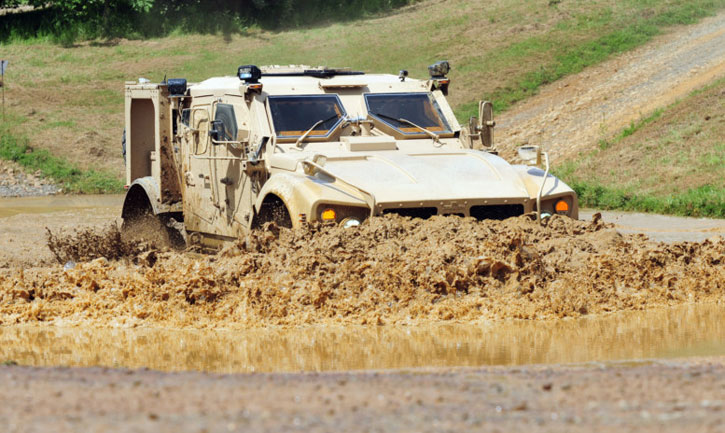
As a provider of survivability and protection solutions for light and medium combat vehicles, Plasan became famous as the provider of armor suits for the up-armored HMMWV, MTVR, MRAP and M-ATV, veterans of the wars in Iraq and Afghanistan. Through these activities, the company specialized in the design and manufacturing of armor kits for modern tactical vehicles, including the Australian HAWKEI, and the American JLTV, to name a few. In these projects, the company implemented the patented ‘kitted hull’ approach, which enables armored vehicle manufacturers and users to obtain the armor kits and assembles them onto their vehicles in the country.

In recent years Plasan expanded its activity to heavier armored combat platforms, including 6×6, 8×8 and tracked fighting vehicles at weight levels up to 45 tons. Such armored vehicles are required to withstand medium caliber cannon threat levels and maintain functionality. According to Kedem, Plasan is already involved in the development of major AFV acquisition programs where its protection solutions are integrated at the vehicle design phase, where they offer the best advantages. Some of the countries the company is currently involved in new AFV developments include Denmark, Spain, Romania, and Israel. “Although all modern armored vehicles are prepared to receive modular armor add-ons, our involvement early in the design phase provides better overall protection, in a solution that is superior to the applique approach used in upgrades,” Kedem said.
The company’s involvement in the early phase of the vehicle’s design enhances the solution’s efficiency, by maximizing protection level, improving ergonomics and augmenting the vehicle’s protection coverage within the gross vehicle’s weight, or providing more payload capacity for the user.
Such armor solutions employ advanced composites and ceramic materials that, unlike steel and aluminum, could degrade their ballistic properties by repeated physical impacts and environmental effects. “As part of our investment in new technologies, we established sophisticated laboratories and ballistic and environmental testing facilities that enable us to explore, test and optimize advanced armor solutions to ensure they meet the user operational profile throughout the entire vehicle’s life-cycle,” Kedem noted.
As part of its armor upgrading solutions, the company also provides enhancements for existing armor, augmenting protection levels to meet threats conforming to STANAG 4569 Vol.1 Level 4, represented by the Russian KPV heavy machine gun series (14.5mm) as a standard – a threat that became a popular weapon with insurgents.

In recent conflicts, Improvised Explosive Devices (IED) and mines proved as a potent weapon against lightly protected vehicles. Such threats have increased the belly protection benchmark for combat vehicles, from the minimum defined by STANAG 4569 Vol.2 Level 1 to Levels 3 or 4, defined by an explosion of a large anti-tank mine anywhere under the vehicle, or even higher. Protection against such threats requires extensive ballistic and blast protection that Plasan is uniquely positioned to meet. To comply with such challenging requirements the company developed advanced underbelly protection structures that retain the capsule’s integrity, augmented by energy attenuating seats that together restrain accelerations and forces to meet the required dynamic response levels (DRI) allowed for the human body to sustain without injuries.
One of the innovative concepts for future armor is the use of sensors to monitor the integrity of the armor. While the technology is applicable for today’s armor suits, users have not yet decided what data they want to monitor and measure, and what useful insights they should obtain. “Our technology demonstrator provides customers a peek into such future capabilities and helps Plasan and its customers assess the potential applications of smart armor for the next generation of combat armored vehicles,” Kedem explained.